Dynamometer Load & Transformer Sizing
Eddy current dynamometers create an eletromagnetic drag on the spinning rotor. The torque is propotional to the magnetic field (which is controlled by the current from the dynamometer controller) and to the rotational speed of the dynamometer. The operating range of the dynamometer is limited by several bounding factors:
- The maximum current supply to the dynamometer. This creates a maximum torque which is below the torque limit of the dynamometer. This is usually only a limiting factor at very low speeds and high torques.
- The maximum torque allowed by shafts and couplers. The linkage components can be safety operated above this level of torque without risk of breaking.
- The maximum heat rejection of the dynamometer. The power extracted by the dynamometer is removed as heat. There is a upper limit to how much heat cab be rejected which depend on the cooling system. Operation above this maximum power will cause overheating and damage the dynamometer.
- The maximum speed of the dynamometer. This is maximum safe peed the dynamometer can be run at. Above this speed there is risk of dynamometer damage.
- The minimum frictional load of the dynamometer. This is the frictional load from bearing and windage of rotating components. Even when no current is supplied this load to the engine test. Ths friction increases with rotational speed.
The safe area of operation of the dynamometer is shown for a 300kw eddy current dyno
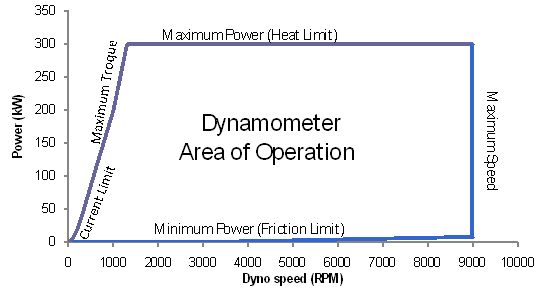
Dynamometer Power Sizing
It is important to match the dyno controller's to the dyno and intended load. Most Eddy current dyno have an internal resistance between 5 and 50 ohms and require 5 to 10 amps at full load and low speeds. Too low a current will limit the maximum power extractable at low speeds. Too high a current will force the controller to operate at very low duty cycles, resulting in poor resolution and control. A large dynamometer which is being operated near its maximum capacity at low speeds will require more current.
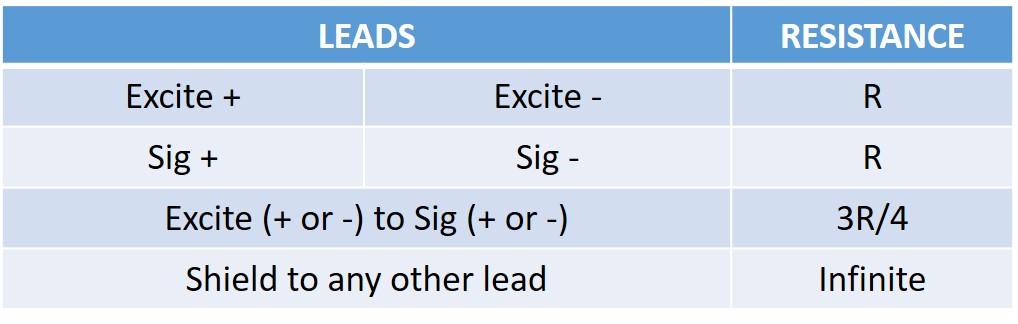